ソリューション
お客様のニーズに合わせてご提案いたします。
前工程 |
---|
前工程
窒化膜ウェットエッチング技術
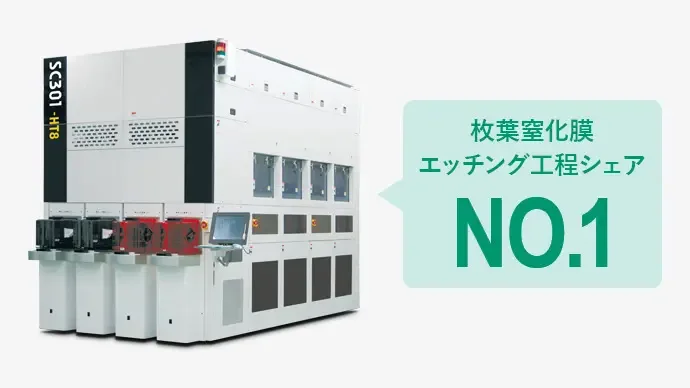
窒化膜(Si3N4膜)のウェットエッチング工程では、ウェーハ表面における窒化膜厚のばらつきに合わせて、エッチング量の分布を積極的に制御することを求められる場合があります。しかし従来のバッチ式ウェットエッチング装置では、エッチング量の分布を制御することは難しいという課題がありました。
当社では、ウェーハ近接ヒーターを搭載した枚葉式の高温ウェットエッチング装置を開発し、ヒーターの設定によりウェーハ表面におけるエッチング量の分布を制御することに成功しました。
半導体デバイスの性能と歩留まりの向上に貢献します。
窒化膜ウェットエッチング技術
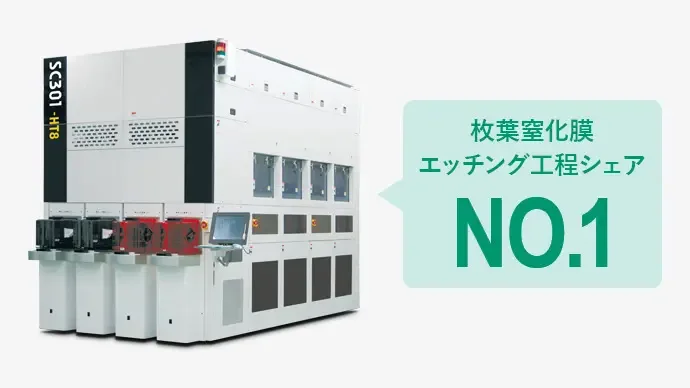
窒化膜(Si3N4膜)のウェットエッチング工程では、ウェーハ表面の窒化膜をすべてエッチングすると下地の膜もわずかにエッチングされるため、そのエッチング量が問題になる場合があります。とくに使用後のリン酸を回収し再利用する場合には、リン酸中のSi濃度が変化することで下地の膜のエッチング量が変化します。
当社では、使用されたリン酸をリサイクルするとともに、使用するリン酸中のSi濃度を制御する機能を新たに追加しました。これにより下地の膜のエッチング量を極限まで少なくすることが可能です。
ウェーハ洗浄技術
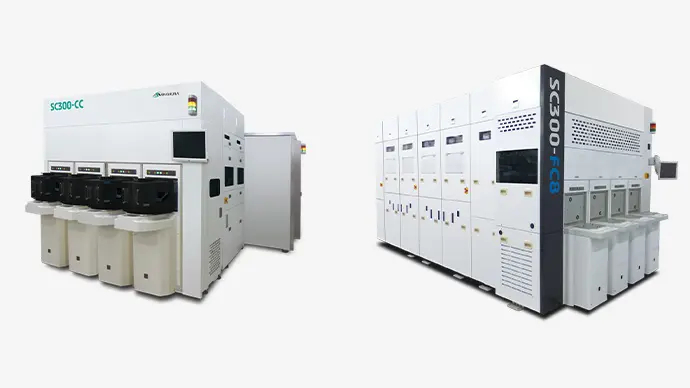
ウェーハの清浄度を左右する洗浄装置にはバッチ式と枚葉式があります。バッチ式には複数のウェーハをまとめて処理できるという利点がある一方で、表面粗さが悪化しやすく洗浄性能が不安定になりやすいという問題があります。
当社では、枚葉式を採用することでバッチ式では難しいオゾン水と希フッ酸の交互処理が可能です。それにより、洗浄後におけるウェーハ表面のエッチング量を厳密に制御し、表面粗さの悪化を抑制しています。さらに、排気効率を高めることで処理室内に生じるミストの影響を解消し、高い洗浄性能とその安定性を実現しました。
プラズマダメージフリーなエッチング技術
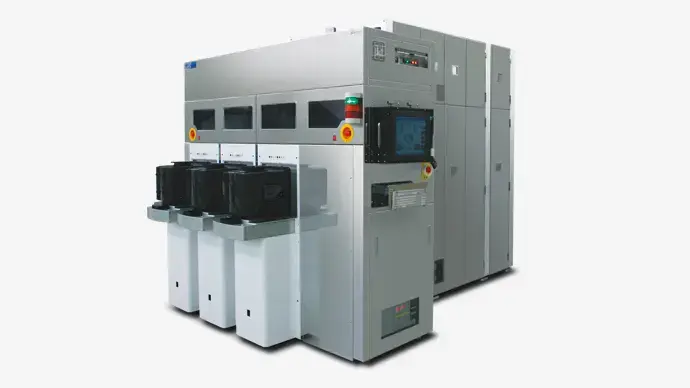
デバイスの電気特性や歩留まりを改善するため、ドライエッチング工程ではイオン衝撃、光、チャージングなどのプラズマダメージを与えずにエッチングしたい、あるいはエッチング後に残るプラズマダメージ層を除去したいという要望があります。当社のCDE装置では、プラズマ生成部とエッチング処理部を分離するリモートプラズマ機構を採用しており、プラズマダメージフリーなエッチング、およびプラズマダメージ層除去が可能です。この特長を活かし、イメージセンサや、SiまたはSiCのパワー半導体を量産する現場で多くの実績があります。
フォトマスクエッチング技術
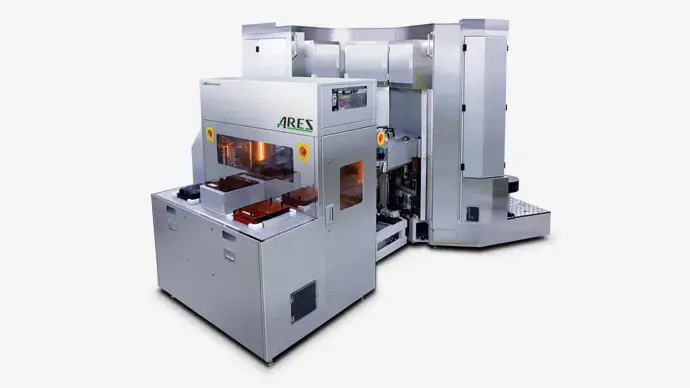
半導体用フォトマスクの製造工程では、様々な配線寸法や配線密度が混在するパターンに対し、その全面を均一に高精度でエッチングすることが求められます。
当社では、エッチングに使用するプラズマ生成部の独自構造とプラズマ分布の制御機能により、パターン全面を均一にエッチングすることが可能です。また、エッチングに使用するガスを大量に導入し大量に排気するシステムにより、高精度なエッチングを実現しています。
フォトマスクエッチング技術
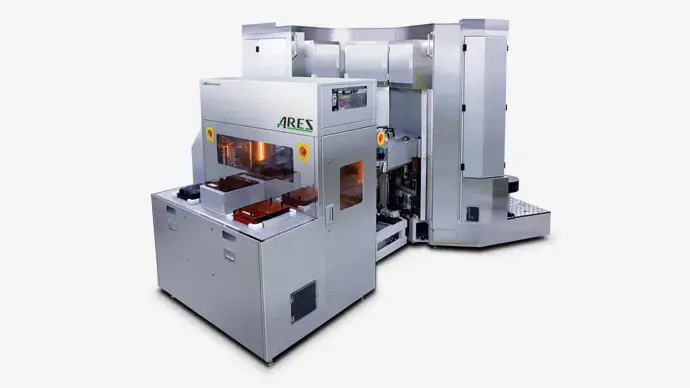
エッチング中に発生する微粒子がフォトマスクに付着すると、それがフォトマスクのパターンに転写されて直接欠陥となるため、エッチング後の洗浄では解決できません。そのため、エッチング中に微粒子を発生させないことが求められます。
当社では、エッチング処理部に生じる堆積物を除去し、浮遊物を排気する機能により装置内部を清浄に保っています。また、エッチング処理部の内面をエッチングや腐食に強い材料でコーティングすることで、エッチングのダメージによる微粒子の発生を抑制しています。
フォトマスク洗浄技術
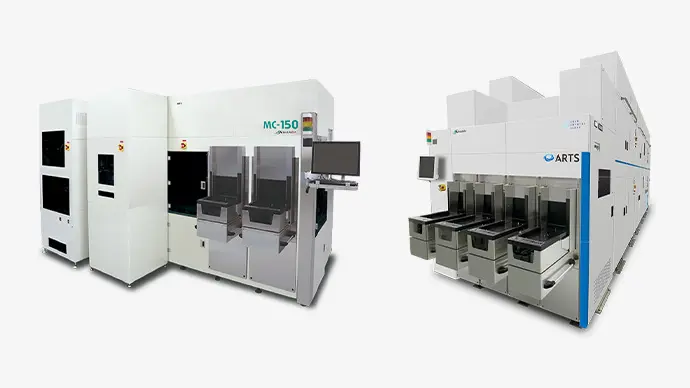
露光原版であるフォトマスクの配線パターンに1か所でも欠陥があると、露光されたすべてのウェーハにその欠陥が転写されてしまいます。そのためフォトマスクの製造現場では、洗浄工程を繰り返すことで欠陥の原因となる異物を除去しています。しかし洗浄力の強い方法を適用するとフォトマスクの配線パターンに欠陥が生じるパターンダメージの問題があり、これまでは微小な異物の除去に限界がありました。
当社では、パターンにダメージを与えずに超微小な異物を除去可能な凍結洗浄技術を新たに実用化しました。水が凍る過程で膨張する特性を利用することで、配線パターンから選択的に異物を浮かせ、排出することが可能です。また、水で洗浄するため、薬液コストの削減や環境負荷の低減にも寄与します。
ランプヒーター併用真空乾燥技術
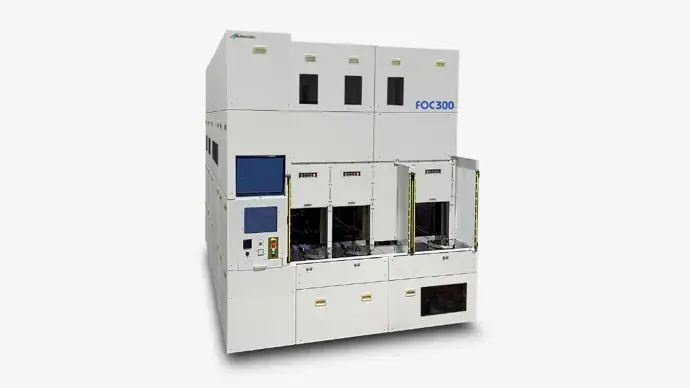
洗浄プロセスでは、ウェーハに面している内部の洗浄はもちろんのこと、DOORのラッチ機構部分の洗浄を求められる場合があります。構造が複雑で乾燥しにくいラッチ機構部分に対し、当社ではランプヒーターを併用した真空乾燥により内部の水滴まで蒸発、乾燥させます。
また、洗浄と乾燥を別々の槽で処理することで待機時間を大幅に短縮し、高いスループットを実現しています。
ひどい汚れに対応する粗洗浄機能
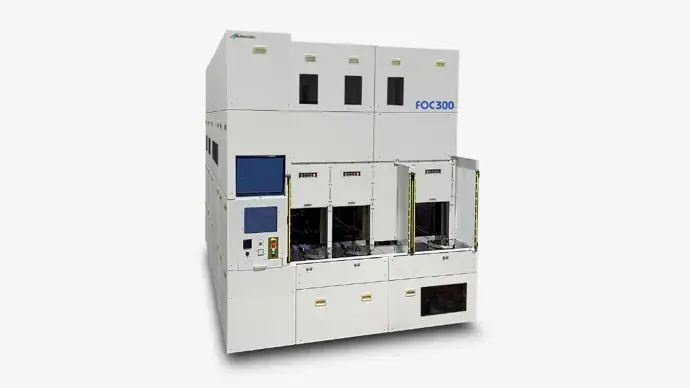
工場外から搬入されたFOUPやFOSBの場合には、外側に大量のホコリやひどい汚れが付着していることがあります。それをそのまま従来の洗浄機に投入すると洗浄槽が汚染され、洗浄能力が低下する問題がありました。そのため、投入前に人手で軽く洗い流している場合があります。その対策として洗浄槽に自己洗浄機能を設け、定期的に洗浄槽を洗う方法が考えられますが、スループットや稼働率を低下させる問題があります。
当社では、受け入れ時の洗浄を行う専用処理槽(粗洗浄槽)の追加を可能としました。外部から受け入れたFOUPやFOSBを開梱後にそのまま投入し、粗洗浄槽で一度洗い流すことで洗浄槽への汚染を防止し、自己洗浄時間を要することなく洗浄処理を継続できます。
洗浄処理後の清浄度確認機能
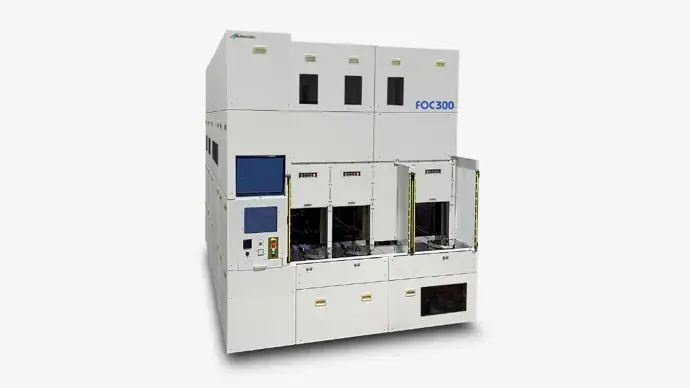
定期的に洗浄処理を行うものの、どの程度の洗浄ができているのか、除去したい物が取れているのかを確認するためには、別の検査装置を使って定期的に清浄度を確認する必要がありました。
当社では、パーティクル数、脱ガスの種類と量、湿度などの測定機能を搭載することにより、清浄度を定量的に確認できるようにしました。
装置内のFOUPバッファ機能
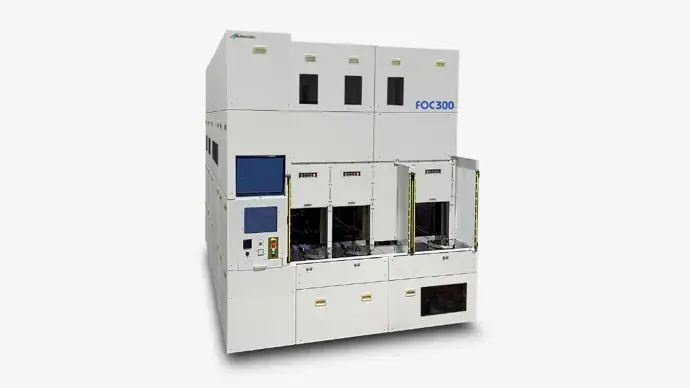
洗浄装置の性能が向上し、高いスループットを得られるようになりました。しかし、工場内でFOUPを搬送するOHTは、洗浄装置の都合に合わせてFOUPを搬入、搬出することができません。そのため、洗浄装置本来のスループット性能を発揮できないという状況がありました。
当社では、実質的なスループットを低下させないため、搬入側、搬出側のそれぞれにバッファステージを用意しました。OHTの搬送タイミングに合わせた搬入、搬出が可能となり、装置本来の高いスループットを実現します。
低温アッシング技術
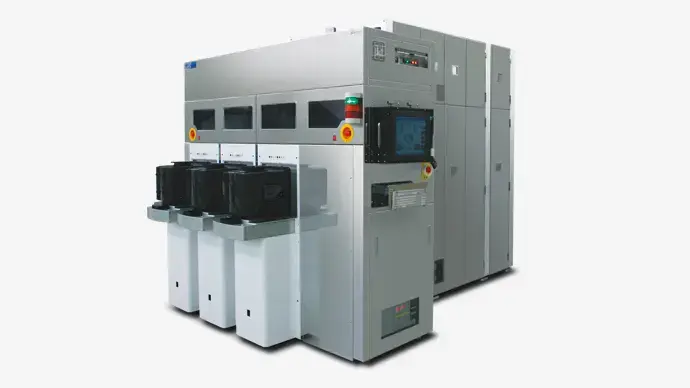
薄化したウェーハをパターニングする工程では、保護材や支持材料が付いたままのウェーハを処理する要望があります。
当社では、高密度プラズマ源と静電チャックを併用し、低圧・低温下でのアッシングを可能としました。
近年はこの特長を活かし、保護材や支持材が付いた薄ウェーハ上に残る硬化したレジストの除去において多くの実績があり、生産性の向上に貢献しています。
後工程
ICチップピックアップ技術
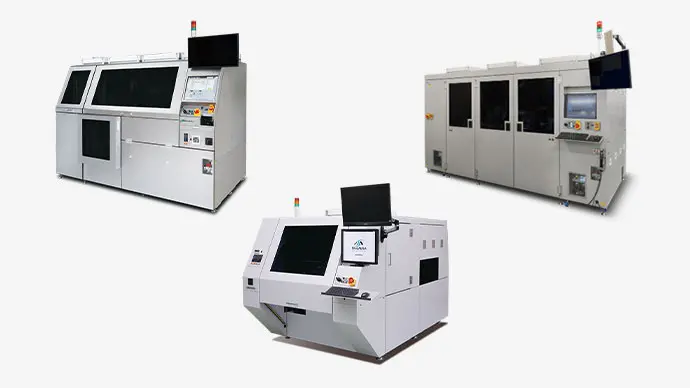
メモリーチップなどではチップの薄化が進み、ウェーハからチップをピックアップする際、チップにダメージを与えてしまうことがあります。これにより不良率の増加や生産性低下を引き起こすことになります。
当社のチップボンダは、独自に開発した薄チップに適したチップピックアップ方式により、薄いチップでもチップへのダメージを軽減させることができます。
高精度ICチップ搭載技術
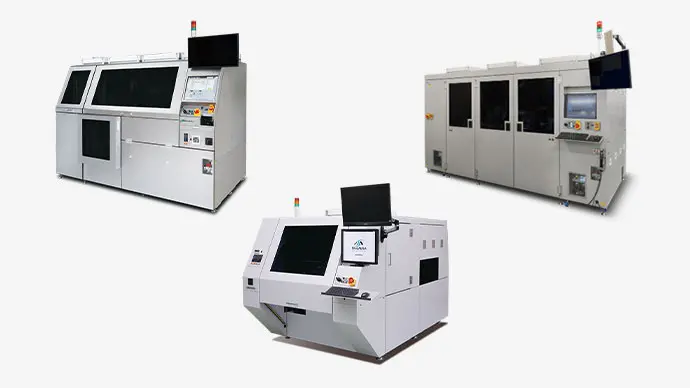
半導体デバイスの高集積化ニーズを背景に、後工程ではチップレット化技術に注目が集まっています。異種チップを最適に組み合わせるSiP(System in Package)の実現が求められています。高い集積度でチップを組み合わせるためには、高精度で安定的にチップを搭載するためのチップボンダの存在が重要になります。一般的に高速で動作するチップボンダでは、各部の温度変化による熱膨張の影響などを受け、安定的に高い繰り返し精度を維持することは容易ではありません。これは大型基板を用いるFO-PLPプロセスではさらに難しくなります。
当社のチップボンダは、生産稼働中に自動で加工点の姿勢変形を検出し自動補正する機能を備えています。これにより常に安定したチップ搭載精度と高い生産能力の両立が可能になります。